Adana HS3 help with the ink disk
Hi everyone,
I was wondering if someone could help me with my Adana HS3 letterpress machine.
I have been searching high and low but haven’t managed to get any answers. I have downloaded the trusty manual which is super helpful from here but I’m just having trouble with the ink disk, ratchet and rollers.
The ink disk seems to be quite high and not allowing the ink disk ratchet to work properly.
There is a metal cylinder that the ratchet and the disk slots over. The rollers seem to reach under the ink disk too so I thought this could be a major sign the machine isn’t set up properly.
Any help solving this would be great and much appreciated.
I’ve attached images too.
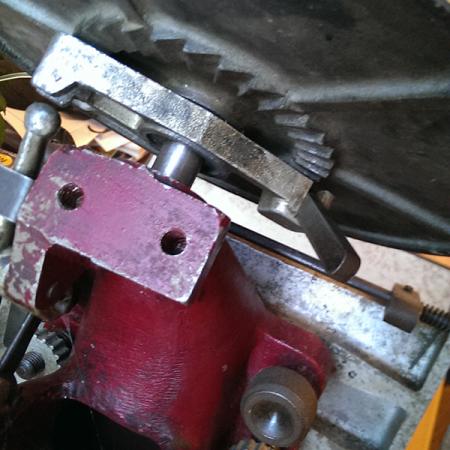
IMAG0090.jpg
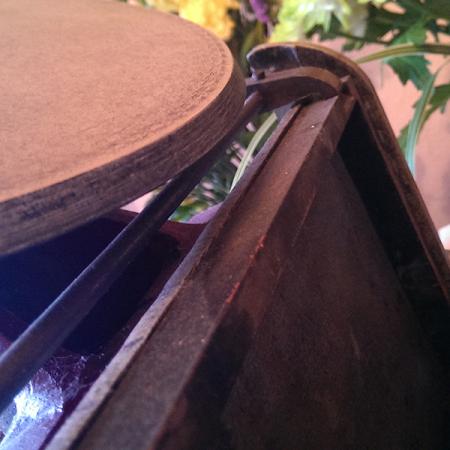
IMAG0094.jpg
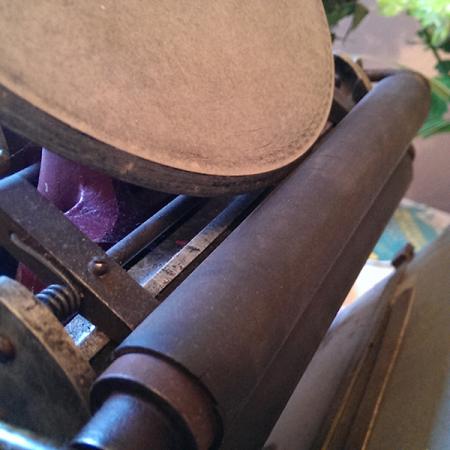
IMAG0095.jpg
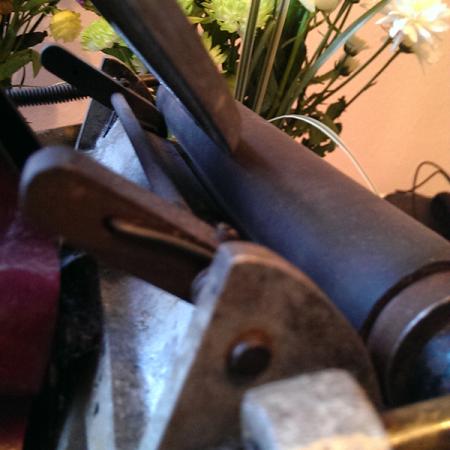
IMAG0096.jpg
The disk should be sitting flush down on the socket but its not.
A previous owner has not kept the disk spindle oiled, a common Adana problem, so it has jammed in the hole.
Somebody has then tried to remove the disk and the spindle has pulled out of the disk.
You have got to get the disk spindle out of the socket, try penetrating oil first to loosen it, if that doesn’t work a bit of heat will be required.
When you have got the spindle out you then have to knock it back into the disk. Be very careful, if you break the disk you won’t find another.
Hi Platenprinter,
thank you for your reply,
The disk and the ratchet spins freely and is easily detached from the socket.
from what your saying it seems like it could be the socket that hasn’t been put in properly. There is a faint mark on the socket which I didn’t realise before - it could be where it needs to be level! oh gosh!
I’ll have to get some oil and do as you suggested to get it out and then correct the socket.
I wonder if the previous owner had tried to get it out and then couldn’t get it back in straight!
If not I’ll try with heat!
A long way off from letter pressing but hopefully she will pull though!
Thanks again! you really helped!
IMAG0098.jpg
C. L. Sir, as P.P. implies the spindle, is normally a press fit in the actual Ink Disc and rotates within the top/base of the machine.
Although I have an H.S. in front of me, which I will sell eventually, I have only briefly checked out the time span and it appears that the H.S.3 was only produced for a short time in the early 1950,s.
In this case the spindle is catergorically press fit into the ink disk and came with 2 (thin) pen steel washers under the disk to set it at the right height for the approach of the rollers!!
The previous owner had the forethought to file a small flat on the shaft, (longditudinally) and a small “V” in the base where the spindle rotates, simulating other parts, on the machine, to assist oil to leech down the spindle, spindle and disk removed occasionally and oiled, i.e. every third/fourth wash up. >>>Probably an oversight in design or manufacture!!!<<<
The machine in front of me at this time, H.S. 3 has the part Number(s) G 1010 & WM 5094 cast into the underside of the ink disk, “part/casting No and probably irrelevant,* But stamped into the base, on the right hand side immediately under the Adana/London Logo are 46 D LU and D I D 424, letter and Number punches, 10 point and 12 point approx. respectively.
Little more info, available if of use, Good Luck Mick (U.K.)
Hi Mick,
Thanks for your reply,
I’m just at the moment trying to get the spindle aligned with hole - I think the previous owner must have taken it out and tried to put it back in but misaligned it, and so it got stuck at a point in a sight angle.
I’ll have to look up the washers and see if I can get them from somewhere too.
C.P. Sir, glad that you are progressing, in the event that you have not yet been able to extract the pin/spindle from the base of the machine, (possibly) lay the machine on its left side, as you look at it, (the frisket bar protrudes to the right) on a soft receiver, foam/cushion etc for protection, machine and work surface!!!
As P.P. suggests, little heat, BUT very briefly!! and not too close!! short bursts, to give the diecast material time to transfer the heat through 360 around the spindle boss.
Preferably with second pair of hands, and judicious use of brass/copper drift, less diameter, than the bore of the stub, and with small copper, nylon or hide Hammer drift your pin out. As the machine base is bored out all the way through the casting, Parallel and not blind!! initially, with your soft hammer and gently of course, try and tap it IN rather than OUT to ascertain if it is moving, with a tiny band of clear tape around the spindle immediately above the base/casting you will ascertain the slightest movement, the tape will act as a tell-tail.
If you already have the stub removed, and you have access to an ordinary vice, grip the stub lengthways, still with some protection on the ends, which are in fact machined with short tapers, with strips of canvas/cloth backed emery or abrasive cloth, by turning the stub perhaps 3 times LINNISH your stub to clean up/out the damage, i.e. as done by all your Shoe Shine *Boys* as seen in all the best Al Capone Movies, Linnishing by another name?? (polishing)
If it transpires that you end up with a sloppy fit back into your actual Ink Disc, measure the depth of the hole in the disc, and then with a pin punch tap a line around the stub of several punch marks to raise the surface fractionally, so that when you reinsert the stub the last, say, 1/4 of an inch makes for a tight fit!!
Washers are not too critical, if availability or sourcing is a problem, at a pinch D.I.Y. manufactured from plastic, nylon even cut up credit card *American Express, of course* will suffice, 2/3 thicknesses of plastic make for beautiful friction free rotation.
It is quite normal to adjust the height of the Ink Disc to suit roller contact more or less!!! … Good Luck Mick
Is the base casting alloy or iron? The concentric wear on the boss looks like aluminum galling. If it is alloy, I’d be careful with the heat.
A.M. thank you for your extra input, the base is cast aluminium, the shaft fitting is bored accurately to accept the spigot, to allow for rotation, the galling, as you suggest is actually the finish, ex production,! mine (with very little use) is identical in appearance, and was probably by design to enable the bottom washer to stand still with friction against the next one(s) up?? to rotate with the Disc.
Re heating, if required, As .P.P. and myself have also implied, HEAT with CAUTION.**Minimum required, as I have also implied, above.
Hi AnonyMoouse - it’s alloy for sure, I’ll definitely watch out when applying the heat. Hopefully I’ll have her working by next week.
Thanks Mike,
I’ve made some of my own washers as your suggestions.
C.P. well done Buddy, the very best of luck, for your first impressions, & results, (no pun intended) hopefully if and when the passion subsides even a little, perhaps post a short resume, (no acute accent available on rubbish P.C.s Sorry. on the Monotype yes!!) for the benefit of all the new ones waiting to take centre stage, and to help them, with what to look for, before biting the bullet. Regards Mick.