Building a Proof Press
I have a small Baltimore Jobber #4 platen press (see attached). It’s small size has been quite limiting, and I’m ready to start printing bigger stuff like posters. However, the size, cost, and logistics involved with finding a Vandercook are more than I can afford, so, with the help of a friend who is a machinist, I’ve decided to build a basic proof press.
I’m not looking for anything near as sophisticated as a Vandercook. My basic requirements are just an impression cylinder, a hand-cranked ink distributor, and a bed that allows for at least 18”x24” prints.
As far as design goes, I’m interested in copying the Hauer Record proof press. See here:
– https://vimeo.com/109147447 (skip to 8:00)
– http://murketing.com/images/signpress.jpg
– http://www.bleisatzkontor.de/WebRoot/Store19/Shops/61750158/490D/F273/CC...
I have watched countless videos online of how a Vandercook works, and looked at as many manuals and blueprints as I could find, but I still have a few questions I can’t quite answer without seeing/using one in person. Unfortunately, there is no one near me who owns a Vandercook.
— What is the purpose of the rider rollers in the distributor assembly? Are they there to allow the vibrator to slide back and forth more easily (sliding left/right over a metal rider roller is far less friction than a rubber form roller)?
— What is the best metal for the vibrator/riders for transferring ink? Is there any advantage of aluminum or stainless over steel?
— I’ve noticed that the form rollers on a Vandercook are geared and roll at a constant rate via rack and pinion, whereas the form rollers on the Hauer Record I mentioned above are free to spin as they please. Is there any disadvantage to having the form rollers roll only when in contact with your form?
— In regards to the Hauer Record, I believe the bar on the top switches between print and trip. Pulling one way lowers the form rollers and raises the impression cylinder (to ink the form and prevent the impression cylinder from getting ink on it). Pulling the other way raises the form rollers and lowers the impression cylinder (to press your paper without inking the back of your paper). Correct? Using only online pictures as a reference, I can’t quite wrap my head around how that mechanism raises one and lowers the other. Can anyone provide a napkin sketch?
If you took the time to read enough to get to this point, I cannot thank you enough…
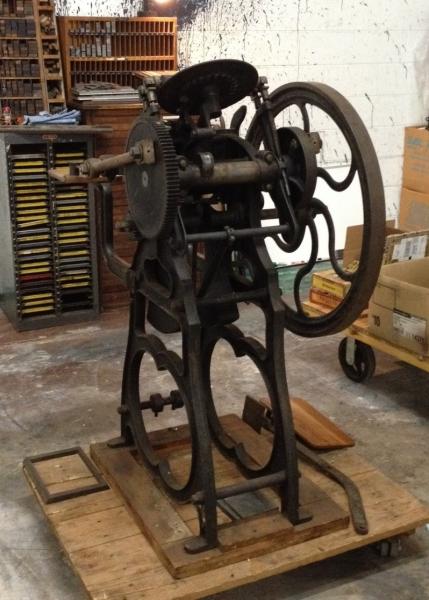
baltimore-jobber-4.jpg
ever thought of converting/adapting an old offset litho press rollers/riders from a press being scrapped-the inking rollers, riders and cylinder could be machined in half so you could get two sets out, or even get an offset press and just adapt the bed to take letterpress………if using polymer then perhaps you might not even have to do that……..stainless steel if possible, more riders the better the ink distribution in the “ink train”
or even adapting converting old conveyer belt rollers….
then get some side frames cut out machined/lazer cut- , perhaps even a conveyor roller cut have a slot milled down it that could have affixed a simple paper gripper system…..just an idea…straight off my head…….
also, regularly in europe these come up for sale-could be cheaper to import proofing press…eg this one been available at least a year..https://www.maschinensucher.de/fy/inserat/suche/Hochdruck-Abziehpresse-Nudel-Haas-Kellhofer-Grafix-GX-1/i-1152470….
also
https://www.maschinensucher.de/fy/inserat/suche/Hochdruck-Abziehpresse-Nudel-Plamag-Plauen-Model-SZ-1/i-1034636
http://www.ebay.de/itm/Druckpresse-Presse-Buchdruck-Handpresse-Abziehpresse-Andruckpresse-Drucken-Druck-/221667383624?pt=Alte_Berufe&hash=item339c67d948
800 euros today
although this has sold quickly, the simple design might prove intresting to you
http://drukwerkindemarge.org/proefpers-mertens/
The typical Vandercook rider rollers improve distribution in two ways: by being full width of the form rollers, they break up the line left by the oscillating roller as it travels laterally; by being of smaller diameter, ghost images are reduced and ink is distributed more evenly. If you don’t have lateral distribution there will be stripes of ink around the rollers.
In any inking system rollers alternate between hard and soft. Rubber goes against metal goes against rubber etc. Vandercooks often have the roller carriages held by gravity and so some weight is necessary; no aluminum rollers there. But if distributor rollers are fixed into the frames as on production presses, you could have lighter surface materials, even plastic.
The gearing is how Vandercooks drive the rollers when they leave the motorized drum. If they aren’t rotating when they reach the form, they will wipe the edges. On a simpler press they could be driven by roller bearers, though that would reduce available form area.
Do you really have to have the hand-cranked ink distribution? I’ve been working on designing a Showcard-type press for myself for the past few months, and if you’re okay with just hand-inking your type, it’ll be a lot less complicated and you can do something like this, just scaled up a bit: http://www.briarpress.org/41110
This Eickhoff proofpress is available for sale in the Netherlands, it’s one of the last series built before the company closed down. Needs some love, care and attention…
eickhof.jpg
Hello windu….
Building a proof press is not that difficult at all. I just built a small experimental press as a test-bed for a larger press that I’m building. It is functionally equivalent to the signpress in your link. Here’s the link to my description of that particular press:
http://www.briarpress.org/41110
It is of course a simple hand-inked machine, but it prints a very nice image, and could be scaled up to 18” wide quite easily.
If I were going to add self-inking, I’d probably use a Showcard-style inking mechanism as in the pic below. It would be rather easy to build, but works quite well.
I’ve built several other presses, some posted here, and so have several other folks. A quick search will bring up quite a few Briar-Press-User built machines that might help you with your designs.
Showcard1.jpg
WCP:
That sound you hear is Opportunity knocking…. :o)
I found this thread very interesting.
I have a Vandercook No2 which came without a feed table, gripper bar or inking system. I have built all 3 pieces. Some of the questions listed above I think I can answer or at least have opinions on having gone through several iterations and failures along the way.
On this question specifically:
— What is the best metal for the vibrator/riders for transferring ink? Is there any advantage of aluminum or stainless over steel?
I don’t think it really matters. I ended up using glass. As someone above suggested using/adapting parts from an old offset press. I used a large oscillating roller off an old t-head. It works very well.
Also saw this which might be of interest?
http://portland.craigslist.org/search/sss?query=letterpress&sort=rel
All the best,
Don
I have an old intaglio press I use for printing my etchings and I have made rails and frame on either side of the bed to hold the chase. Due to he fact that the roller is steel, I lay down a sheet in Lino on top of paper so it has a little give and run the entire thing through the press. It works quite well.
Thanks for the responses everyone.
parallel_imp: That all makes sense. Thank you so much.
Winking Cat Press: That Showcard inking mechanism looks pretty simple. Did you build the bed of your press out of metal or wood?
You can see in the photo below that there are two little ridges at the end of the rails that the form rollers pop up onto. Can anyone explain how they stay raised, and then how they drop down once the carriage reaches the opposite end of the track?
Andrupre_Hauer_2.jpg
Wind-up- Yes, the bed of the small test-press were made of thick laminated Birch Plywood. If used in thich sections (greater than about 1.25 inches) the material is quite stable. The rails are hardwood.
The raising of the rollers you describe are part of the trip mechanism. I’m not familiar with that particular press, so I can’t comment on that particular one. BUT with the seperate Showcard inking system, you can eliminate much of the complexity.