Windmill Motor
I just picked up a windmill with factory foil from 1985!
I know the motor is 3 phase, but I want to find out if anyone had an idea if the motor could be driven with a 1 phase to 3 phase inverter.
Thanks!
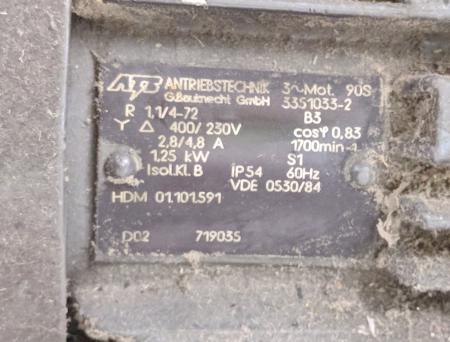
Motor Plate.jpg
ffi |
fl |
5m |
4m |
|
k |
e |
1 |
2 |
3 |
4 |
5 |
6 |
7 |
8 |
$ |
@ |
# |
Æ |
Œ |
æ |
œ |
|||||
j |
b |
c |
d |
i |
s |
f |
g |
ff |
9 |
A |
B |
C |
D |
E |
F |
G |
||||||||||
? |
fi |
0 |
||||||||||||||||||||||||
H |
I |
K |
L |
M |
N |
O |
||||||||||||||||||||
I just picked up a windmill with factory foil from 1985!
I know the motor is 3 phase, but I want to find out if anyone had an idea if the motor could be driven with a 1 phase to 3 phase inverter.
Thanks!
Motor Plate.jpg
Numerous discussions on the site. http://www.briarpress.org/44924#comment-66719.
Mine works well with a Danfoss Microdrive but there are lots of options.
I just worked with an electrician on this issue and they were awfully hesitant about a phase converter! Which was a big bummer to me, so I will be curious what you decide.
For my situation, I was setting up in a city building that HAD 3-phase that had just been weirdly wired (split to power two storefronts) so they were able to reset the 3-phase for us. This was obviously the more expensive option but it seemed to make sense, so hopefully I didn’t get bamboozled. :)
From an engineering standpoint, Phase converters work just fine, although there can be some inefficiencies. From an electrician’s point of view, standard three-phase is superior, plus he gets some business out of it. You didn’t get snookered, you just took the electrician’s conservative approach, especially since it was so (relatively) easy to do. Anyone without three phase nearby will probably find VFDs to be the best option.
Michael -
I would not recommend that you spend your time or money dealing with producing 3-phase power for the motor you have. I suggest you replace it with one that will work off of your currently available current.
The Windmill only requires a *continuous duty* 1.5 hp motor running at 1725 rpm, drawing 10.4 amps at 220v.
Costs range from $75 (questionable) to $200 - $300 for a reliable, continuous duty agricultural motor - designed to run farm conveyors or fans all day long without overheating.
Wired at 110v, it would still require a good 20+ amp circuit, which is pretty common in homes, garages and workshops these days. But 110 volts will do - if you have the amps. 220v is better - IF you already have the circuit in place- which is why I didn’t bother going to 110v myself.
A phase converter - and installation - would likely cost quite a bit more, unless you like to play with motors and want to make your own or have an electrician friend willing to do it for you. (Of course he may also recommend what I’m saying here…)
My Windmills are wired for 220v, but could also run on 110v. The difference is the amperage draw - and the corresponding wire size required to carry the amps - and the corresponding impact on your electric bill.
But that only matters if you’re planning on running the press all day, every day.
I changed my motor about 20 years ago, and the replacement was a used 220v motor which cost me about $100.
The “proper” motor also requires a “jump-start” booster circuit to give it extra current when starting up, but my motor guy wired in an external switch for me to save money.
In practice, I press two buttons to get the motor started, then release the “starter” button once the motor is running - about 5 seconds… I actually used an old car horn button for starting - and only replaced it when a classier-looking industrial momentary switch fell into my hands. I’ve started my press this way for the past 20 years of occasional operation with no problems or inconvenience.
3-phase 220/440v motors are indeed the most efficient (draw the least amperage) - when run as three-phase via a dedicated 3-phase circuit - as was the case in large industrial plants.
But a phase converter wipes out any such efficiency; you may plan to input 110v or 220v single-phase to produce the 3-phase output your motor requires. Doesn’t make much sense to me considering the alternatives - and may draw a lot more amps in the long run…
Calculate your current draw and costs…. It’s all amps or kilowatt hours. Figure 100 kw per amp and you can ballpark the figures you need.
The Windmill motor runs at a constant speed. Speed is controlled by the diameter of the pulley on the motor shaft. It changes diameter based upon the adjustment made using the handle the front of the press.
What I recommend you look for as you research phase converters is a 1.5 hp, 110v 1725 rpm continuous duty motor with a 5/8” (I think) shaft - in any case, same shaft diameter, form factor and type as the motor now mounted on the press. The specs should be clearly marked on your current motor.
You may be surprised at how reasonable this approach might be compared to converting your available power to 3-phase…
Also - remember the current draw listed is max - undler load. A Windmill spends most of its time idling - with almost no load - and drawing very little current. It only begins to draw more current when it’s actually making the press move - and getting work done…
Let us know what you come up with.