Deep, crisp impression off a tabletop cylinder press (like Showcard)?
Hi everyone,
This question goes out to owners and those experienced with the Nolan, Showcard, Signpress, or the Dick Blick Magnetic Press (not the heavier galley proof presses).
I understand that cylinder type presses such as the Vandercooks often give the best impression due to the single line of contact from the cylinder (similar to an etching press). Is this also true of the signpress? I have read some people only getting a kiss from these presses and others who use tympan to get a deeper impression.
My question is this: If the signpress has a decent paper gripper is it possible to exert the type of pressure required to get a nice impression while also creating a crisp image and decent ink coverage on the print?
Also, I noticed that some of these presses have hand dial adjustments for thicker or thinner paper and I’m curious as to how this actually works. Does it raise the roller off the rail bed? And is there a trip like mechanism so that you don’t get a double impression on the ride back?
I’m interested in buying one but want to hear the general consensus before hand.
Thanks!
IMG_1261.JPG
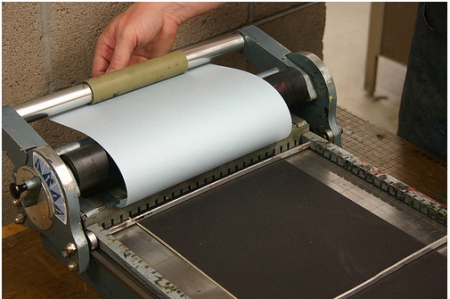
Picture 3.png
The press in the second picture seems to have a rubber layer over the cylinder. I don’t expect you’d get a debossed print with a setup like that.
Daniel Morris
The Arm Letterpress
Brooklyn, NY
Hi Daniel,
Thanks for the reply. If the rubber was replaced with a steel cylinder like the attached picture would that be more likely to get a debossed effect?
12_inch_bench_press_portable_fs.jpg
That new image is an etching press. You’d want some type high bearers to keep from smashing everything and to keep the pressure even across the bed. Are you asking about a particular press, or are you thinking of making one?
Dan
The second picture is mine.
I can say without a doubt, that you can get some impression from a Signpress or a Show Card. As to deep and crisp… I think that is beyond what these presses are capable of. My signpress will adjust for paper thickness, but even running on the thinnest setting, it is still pretty touchy for even impression when I print a large cut or form.
I also have an etching press that I use for relief printing. It will make a deep crisp impression all right, but like Dan mentioned, I use roller bearers. My etching press is a Dick Blick 999 model, also marketed as a Richeson. It sells about $1k and has a tall enough throat to print type high. If you were using something like this, you would also want to construct some sort of paper registration system. The rolling upper cylinder has a tendency to slide the paper across the top of your form. Printing paper on the bottom does not eliminate this problem, in fact it makes it worse. I first began to explore letterpress because of this paper slippage.
Thanks for the replies everyone.
Daniel I sent that other picture just as a reference to the metal cylinder. Since I don’t have room for a Vandercook my inquiry was if it would be possible to get a decent impression and quality from a purchased showcard press if I tweaked the settings.
Boundstaffpress - What I liked about the Signpress you have is the fact that it seems like there’s some sort of mechanism to prevent a double impression on the way back. Where did you find your press?
Thanks for your answers everyone.
I would like to add to this discussion. I hope I don’t cause a brew-ha-ha by doing so.
We have a large Showcard press at the college where I teach. Bed about 24” x 36”, maybe larger. As you may know, the roller height is completely adjustable with the adjustment knob at the head of the press. We printed an edition of 20 copies, 3 pages size 15” x 22”, using 36 pt and larger type. The participants wanted a deboss so the height was adjusted to do that. A couple of lines of type were even blind debossed. We printed on either Somerset or Copperplate 100% cotton 300 gsm paper, dampened and dry. Everyone was pleased with the results. Of course, the usual disclaimer about wearing out your type and damaging the press applies. But it can be done.
n/a
Thanks for commenting longdaypress. My experience has been with the Signpress, and not a showcard. I was making assumptions that they were the same.
Good to know that you were able to achieve successful debossing results with your press. I think the rubber roller on mine limits the control of debossing.
Mike - I saved my press from the scrap pile when I cleaned out an unused classroom at my school. Just last week, I discovered the Signpress brand table that came with the press is still in the building.
Always someone who has to say “You’re doing it wrong.”
When I print on my etching press, I use a “blanket” for relief printing. This blanket is just a self-healing cutting mat. It has enough give to protect my cut, and printing press.
Repeatability is always important with any relief printing method, letterpress included. Make efforts not to damage your press, type or cuts. You can get deep impression without damaging you materials. You just need to be aware of the limits of your equipment and supplies.
When I was learning to print in the early 60’s, any impression on the sheet was frowned upon, today people want to see impression and that’s ok but like Paul says most if not all presses were not made for this, as was most type, poly plates are fine for beating up, but some of this type can not be replaced and will be gone forever. I bought a rubber stamp co. in the 70’s, all type was foundry, when you heat up the type and punch it into the board it really flattens it, we would proof the type first before we made the stamps, about one tenth of the type didn’t print and was thrown out, so we bought a ludlow so we didn’t have to worry about smashing all that foundry type. If you must smash type at least smash ludlow type, just my feelings on this, who’s to say who is right or wrong. Good luck Dick G.
n/a
Being originally a printer of linocuts and etchings on a cylindrical press, I came late to letterpress, but now own both kinds of presses. I have printed from type on the cylindrical and printed linocuts on the letterpress, and of course the reverse! Coming from this direction it is easy to understand what boundstaffpress is saying because it is understood that blankets are part of the printing process for us. For pure letterpressers I can understand your reluctance. But it can be done on an etching press with a proper base and spacing — several of us do it all the time without ruining our equipment and materials!
In this day and age, we need to support experimentation and creativity or the computer will eliminate printing presses all together. mikeyheu, experiment away but use common sense and the suggestions from all.
n/a
I have run my print shop full time from my home since the late 90’s , most of the printing i do is letterpress, not because its cheaper, but i like printing from type. When i run envelopes on my windmills i tape a offset blanket on the platen, it saves lots of makeready time, but like Paul says it will wear the type pretty bad, i thought it was a good idea at the time, but it really rounds the letters, most of my type is ludlow, so i just cast extra lines and change type . Just because you use a rubber blanket doesn’t mean it will solve your problems, my first liontype job was in 1966, in a 2 man typesetting shop, there was a poco proofing press there, one of the first jobs giving me was to change the tympan to a rubber blanket, worked there 3 years and proofed hundreds of galleys with this, 10 years later i bought a small rubber stamp company, and there was that same poco with the same rubber blanket. After nearly 50 years i still use that poco with the same packing and same rubber blanket, but only for proofing type to check my spelling. My point is for a couple of copies its not a problem, but for extended use rubber will definately round your type. Good Luck Dick G.
From what I’m hearing the use of polymer plates will be the best route if I want to keep my type intact.
What if the adjustable type presses were set exactly to line height and a sheet of tympan was placed over the top? Would this be able to “protect” the type?
I guess what I’m trying to understand is if the principle is the same in terms of the cylinder presses (i.e. Vandercooks versus Showcard), why can’t the same results be achieved if the cylinder is set to print at type high? Or does the Vandercook also wear down type over time?
Best,
Mike
Any press will wear type when you try to achieve a deep impression. experiment with your press with different stocks, try a sheet or two of a vellum card stock over the paper your printing on, use a old plate or cut that you don’t mind wrecking. most of the sign presses the handle will flip over to raise the cylinder so you can return it without double printing. Good Lcuk Dick G.
Thanks everyone for your comments and input.
I believe that’s my line-0-scribe in the first picture! I got it and did some experimenting and then found a Poco so haven’t used the line-o-scribe much. It prints linoleum block well and will make a deep impression with type but it is kind of difficult with type. It does get a deep impression but inking is hard to get perfect and I found that I didn’t like the fact that the roller has to either go back over what you’re printing or some sort of waste sheet needs to be in for the return. I sort of solved that by not using the little gripper mechanism and then I can print in each direction. I rigged up a sort of hinged device to hold the paper and register it which I lock into the bed. I think the Poco does a much better job.
Just a quick comment. The Showcard and Linoscribe types of press require that you manually pull the cylinder over the form and the deeper the impression your are trying to achieve, the more pressure (read: harder to pull!!!!) is necessary. With a proof press like a Vandercook or Poco, the cylinder is cranked over the form and much greater pressure (depth) can more easily be achieved.
I’ve been working more with my lineoscribe and have now a great respect for what it can do. I’m printing an artists book with type (polymer with boxcar base) and etchings. I printed the etchings on an etching press and then used the lineoscribe to do the text. After trying my Sigwalt (wide paper problemmatical), the poco (but registration was overwhelming) so in desperation tried the lineoscribe. I locked in a large boxcar base with quoins. I planned to trim off 1/2” of the paper so I clipped the paper into the paper holder clips. Then I had to work out roller bearings. I double stick taped two long pieces of leading together. They were long enough to span the entire 12” side of the boxcar base. I later layered on one layer of strapping tape to raise it just a bit higher. I made two of these and put a length oftape across one end of the boxcar base with just enough room for the bars to slip under. I put a layer of tape under so it wouldn’t be sticky except at the ends which were taped to the boxcar base. Then I made a sort of weight for the loose ends out of heavy slugs stuck together long enough to span across from one bearing to the other so that when I hand inked the bearings wouldn’t lift and move around. The sequence would be: insert the bearings either side of text, weight the ends, roll the ink, remove weight, remove the bearings, insert paper and packing, roll press. I used damp paper and inked with a hand brayer and got very nice results. Deep impression but not too deep. Oh, and I used a little masking tape to mark where the edge of the paper should fit into the clips. Because my studio space is quite cold until I show up and turn on the heat, I was having trouble with the ink. It was better with some linseed oil. On a whim I used Caligo water soluble oil relief ink and got even better results. Just wanted to correct my earlier comment because now I think I can do a lot with the Lineoscribe.
Very informative post. I believe presses are important tools to use when making paper crafts such as cards and letter heads. Like you, I am also partial with the Signpress since you can make a lot of adjustments on the device unlike the other types of presses.Halloween