Ink streaks
I cant seem to get rid of these streaks (see attached image at the top). It seems to be the “JWM” leaving streaks. I’m printing on a Kelsey 5x8. Any help is greatly appreciated.
Thanks,
Tyler
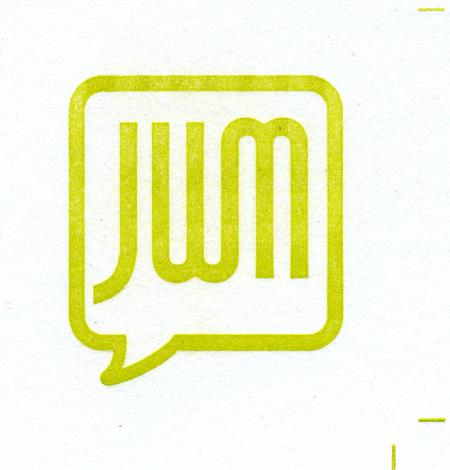
Untitled-1.jpg
ffi |
fl |
5m |
4m |
|
k |
e |
1 |
2 |
3 |
4 |
5 |
6 |
7 |
8 |
$ |
@ |
# |
Æ |
Œ |
æ |
œ |
|||||
j |
b |
c |
d |
i |
s |
f |
g |
ff |
9 |
A |
B |
C |
D |
E |
F |
G |
||||||||||
? |
fi |
0 |
||||||||||||||||||||||||
H |
I |
K |
L |
M |
N |
O |
||||||||||||||||||||
I cant seem to get rid of these streaks (see attached image at the top). It seems to be the “JWM” leaving streaks. I’m printing on a Kelsey 5x8. Any help is greatly appreciated.
Thanks,
Tyler
Untitled-1.jpg
Hi, Tyler—
You can try several things:—
1. Double-roll the form—that is, ink it twice over with the rollers for each sheet printed.
2. Turn the form ninety degrees, or cant it slightly in the chase with spacing material and put your guides at an angle to keep the printing straight.
3. Mix your color with opaque white rather than transparent so that you can carry more ink.
Hope these suggestions help, Brian
I tried double rolling it. However, when doing so the small type fills in (7pt.). I did mix in some trans white. I’ll have to try opaque white. Hopefully that will fix the problem.
Last resort I’ll try the “turn”. I working with a 5x8 press using a boxcar base so I don’t have to much moving, turning room.
Thanks,
Tyler
Hi, Tyler—
You could try printing the small type in a separate pass with lighter coverage if they are over-inked when printed with the cut.
Sometimes one sees color strips printed on the sheet past the trim that are positioned in such a way as to equalize the amount of ink carried across the rollers. That is, the coverage is even across the roller, the off-trim strips compensating for the counterspaces of the printed design. (I hope this makes sense—undoubtably there’s a better way to explain the idea. And I’m not sure how you could apply it here anyway.)
Brian
This is a common problem with small presses, both letterpress and offset. The streaks are caused by ink starvation on the rollers. Ink is removed by the long vertical lines of the letters, leaving heavy ink in-between the letters. Rotating the plate 90 degrees like Brian suggests should help. If you have room to rotate it 30 or 40 degrees it may work even better.
good luck
-edd-
Folks, the form is more or less as wide as it is deep. The letters may get improved inking by rotating the form, but the frame will be just as ink-starved because the form is considerably longer than the diameter of the rollers. This is a case of a form too large for the press, especially if there is also small type not shown in the picture. On a larger C&P a bias chase might be the answer, angling the form off so the rollers have better coverage.
Are crop marks and trim really needed? Smaller stock, or a smaller plate on the base, might allow slight angling.
parallel_imp,
Your exactly right about the form being larger than the diameter of the rollers. The “JWM logo” measures 1.5”x1.3125 (roughly) and the rollers diameter measures 1.25”. I have attached the entire card layout and the set up I am running.
I don’t necessarily have to have crop marks if they are limiting the proper printing space. I just thought it would make registration and final cut down easier. I’m open to anyway to make it work????
Is there a way to position this so that it works and prints relatively well.
Once again I appreciate all the help!
Tyler
DSC00827.jpg
Untitled-1.jpg
Hi, Tyler and parallel_imp—
Maybe I just haven’t had enough coffee yet this morning, but isn’t the critical measurement the circumference of the rollers, not their diameter?
I’m reminded, in this regard, of the unlike form rollers of later model V-50’s, and also of the Little Giant’s form rollers set at an angle across the bed.
Best wishes, Brian
I was thinking of cutting the polymer plate in half (see lock up image above where black dotted line is) and flipping it vertical. Not sure if this would fix the issue but from the post I have read above it seems like it might.
By cutting it I could run the “JWM Logo” in one pass and the small type in another. I know it would create more work but I’m more concerned with making the business cards look good. This way I could keep my crop marks. To keep them in register I could just realign the cut edge of the polymer plate when printing the small type.
Does anyone see a red flag with doing it this way before I go hacking stuff up?
I gotta’ agree with Brian. The circumference of the rollers and the short path across the form can’t carry enough ink for this image. Look also at the horizontal top border above the vertical lines on the sides — the image is starved there as well.
Is it possible on this press to roll a brayer sideways across the form before making the impression?
I’m not understanding this at all. If the circumference is to travel across the form than I would have enough roller area to cover the “JWM Logo”. Am I wrong with this assumption.
The roller diameter measures 1.25”. If my calculations are correct the rollers circumference would be 1.25 x 3.14 = 3.925—enough to cover this logo.
I know small Kelsey presses aren’t really good for printing much but surely they can print a small business card one up?
This is my interpretation of the aforementioned. I’m not implying this is right so feel free to correct me.
Thanks,
Tyler
before you cut the plate maybe you could make a frisket and just run the logo by itself. dick g.
Excuse my ignorance but what’s a frisket and how would one make it?
n/a
put a piece of paper across your grippers, make sure the grippers are away from your gauge pins and the type, then print on the paper, cut out what you want to print, the rest will print on the paper, sometimes if its a long run i use shipping tape so the ink don’t go thru the paper. make sure you tape the paper to the grippers. this also is used to help pull paper off of a heavy form. good luck dick g.
The rollers come off the ink disk with a full load of ink and travel down over the form, then they travel up over the form with less ink in the image areas, resulting in streaking. You should try angling the plate as suggested by Devils Tail.
When I angle the plate the crop marks hang off the base. Should I cut around the polymer plate so that I can position the form angled near the edge in order for my gauge pins not to smash the base? My sheet size is pictured above which leaves just enough room for gauge pins.
I really appreciate all the help. I apologize if I am killing you all with so many question. I’m fortunate to get insta-help!
Tyler
devils tail i think is right, by angling the plate it should help,i would try that first, dick g.
n/a
Awesome!
What about the questions above regarding the crop marks/cutting the plate/gauge pins smashing the base?
n/a
Gotcha!
Thanks Paul and to all the others for the help.
Tyler
Of course I mis-spoke when I used diameter instead of circumference (a hazard of 5 a.m thought). But now seeing how small the form actually is, I woud say it is mechanical ghosting but not from too large a form for the roller.
It isn’t hard to understand if you watch closely. Look at the image left on the top roller after it passes the form on the down stroke. Then watch it as it comes over the form on the upstroke. The form and roller-image seldom align perfectly, and where the ink-starved portion of the roller goes over the form, the ink is lighter; where the still-inked portion of the roller hits the form, the ink is darker. (The same happens on a roller too small for the form, but in more than one continuous revolution over the form instead of on up and down strokes.)
Angling the form may help, or it may make for angled ghosting (which still might be preferable). Alas, there are no rider rollers for tabletop presses to break up the ghost image; that’d be a money-maker today!
This is an example of how a large base on a small press makes for unnecessary complications. You wouldn’t have to feed an oversize sheet or trim after printing, but just print on a final size card. Wooden wedges (or “Any Angle Furniture”) would allow angling of a smaller base, and stock is easily angled by the gauge pins, without smashing anything. For a business card, Elrod-cast lead high-base (at .854 or .875 depending on which Boxcar plate) would work just fine. Without a printer’s saw, Elrod strip can be cut with a hacksaw and dressed on a hand miterer set at 90 degreees.
On a small press you need a lot of flexibility when attempting large press results, and a big base takes some flexibilty away.
In any case, heavy solids and small type can’t take the same amount of ink without one or the other suffering.
Here’s a link to a site with a home-made rider roller for a C&P. Maybe one can be made for a Kelsey?
The author used an old rubber roller from an offset press. The riders on a Kluge are metal.
http://www.twopiglets.com/kluge/parts/
For this particular inking problem a simple rider might not remove the ghost. The oscillating riders made by Triumph and Acme for C&Ps had a slight lateral movement, and that would help replenish the ink-starved strip on the roller. Those riders clamped onto the upper saddle, or had flanges slipped under the ends of the rollers, depending on what position they ran (that is, whether between upper two or lower two rollers). These were made for C&Ps but they would fit other compatible Gordons. The roller saddles on Kelseys would require a different method of attachment, and it’d have to be a method that wouldn’t add to the roller-sliding problem common on Kelseys. Any rider would also have to clear the grippers, which as I recall sit rather close to the rollers.
Brian - So. What did you do? Did the job get done and look the way you wanted.
Sorry to come in so late, but here’s my 3 cents’ worth:
(even if it is too late to help you on this job…)
========================================
Why not just slap that plate on at 45 degrees to eliminate the banding problem? An idler roller, would be great, but is impractical on press that uses roller hooks like the 5x8. Double inking, opaque white and larger diameter ink rollers are great ideas, too but slapping a pp plate on a 45 degrees only takes a minute..
But for the gauge pins, use Megill Flexible Gauge pins or simply cut little slits in the tympan like this: http://www.excelsiorpress.org/reference/presswork/smallpresswork.html#se...
Roller bearers could also help if you encounter any slurring on the edge of the form.
And as far as the heavy solid/light text issue - make ready! Build up behind the solid area, keep pressure light over the small type. With proper inking, you can have both the solid image and small type print well.
- Alan