Impression problem
Hello.
Our company purchased a 10X15 windmill for die cutting in general.
From the very beginning, I had a problem with the strength of the impression.
I changed the shear collar as it showed microcracks on the inside.
However, there are still huge problems with aligning the impression. (photo 1)
The die-cutting plate is 0.8mm thick and you can see it (photo 2). The impression on the top is much stronger, but I am more worried about the difference between the left and right sides.
Has anyone encountered such differences ???
I would be grateful for any suggestions.
With greetings from Poland.
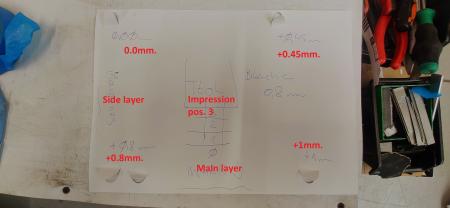
zdjęcie.jpg
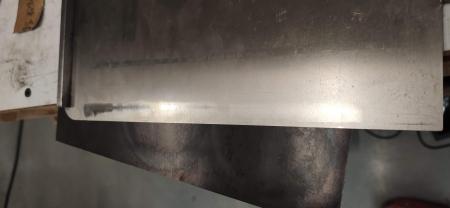
Płyta wiatrak.jpg
If the top is getting more pressure , then you need more packing behind the cutting plate. Don’t forget that packing still needs to be set to match the recognised Heidelberg requirement 0.040 thousand’ths of an inch for Uk imperial measurements.
For the side to side issue you may have to make a make ready sheet to go under the plate which can be used for every job.
And, in general, the packing should add up to the thickness of that little slot in the top of the right-hand delivery pile guide. Too little, you are screwing in the impression to the point that it’s heavy on top; too little, you get impression on the bottom. As for difference side to side, be sure that there’s nothing on the left side to interfere with the bearer on the chase edge.
Frank.
Your pics, even tho they make sense to you in real life, are not depicting the problem very well. I have never had to align a windmill platen left to right, but i would grab onto it and see if you can “Twist it”. Check for looseness. Better Heidi mechanics are here I am sure. For now, I would just make a permanent packing layer to even the pressure out, and do a separate makeready sheet for each job.
If in fact the impression is soft on the left side, this might indicate a problem with the platen shaft and/or the bearing in the swinging platen. This area may not have been getting oil, due to blocked or crushed oil tubes. The result would be a “spongey” impression, and there would be no economical cure for this condition.
The fact that the shear collar was cracked indicates to me that at sometime in the past this press had an incident which resulted in considerable damage. There might be scars from that, somewhere.
Good luck with your correction efforts!
Frank, Ercim, thank you for your reply.
Frank, I know that I need to pack substrates under the plate
… As for difference side to side, be sure that there’s nothing on the left side to interfere with the bearer on the chase edge.
I’m sure there’s nothing interfering …
I know that the machine is not new;)
For sure I found some slack on the T0306 sleeve (two halves).
My friend and I tried to move sideways, there is no slack, it won’t even budge.
Going back to the thickness of the typman, I know to be 1mm. (imp. 0.04)
However, the difference of 1mm (0.04) diagonally is very strange.
Link to the video showing loosened bush.
https://photos.app.goo.gl/SQnGwNEU7MhDqafD7
Thank you again for yours advice.
Gerro, I was thinking of your problem today. It came to me that some time in the past I had a chase that gave me a problem. I found it and put a micrometer on the bearer of that chase. That 1 chase measured .960 thousands. I measured my other chases and they all measured between.903 and .910 Out of a total of 26 chases measured 11 of them were .908. The one chase that was .960 I believe was for a foil stamping machine. Maybe you have such chases. The chases I measured were E meaning English .918 machine the .960 was maybe for an European machine.. Hope you figure it out. I watched your video I don’t think that loose bush is your problem…but then I’m no mechanic Good luck to you Bud
Ok guys!
Everything is already known!
Today I took chase measurements and the difference between Grafopress chase vs Heidelberg chase is 1mm. (0.04)
The machine comes from the Dutch region ,
after adding the missing 1mm. behind the die, everything is fine.
There is no longer a difference between the sides
pic 1 Serial number
pic 2 Heidelberg chase
pic 3 Grafopress chase
I would like to thank you all for your help.
serial Heidelberg.jpg
Rama Heidek.jpg
Rama Grafopress.jpg