Registration marks
A recent note asking questions about how to register plates made me think it might be worth mentioning how we do registration marks at Lead Graffiti.
We like having a ‘corner’ to match to so we produce a zigzag line at each corner. We have a couple of templates we can grab from to start a new file. Some only have a step of 1/8” (business cards & other small pieces) and another has 1/4” (posters and long wedding invites).
The crop marks are made using the “registration” black so they will show up on all plates.
We went to Fulton Paper (that’s here in Newark, DE) and bought various sizes of Ziploc bags. We always try to group projects together when we make photopolymers from Boxcar and they usually come in hugh sheets with the various plates all mixed up.
THE FIRST THING I DO WHEN I OPEN THE PACKAGE is trim everything down.
Depending on how much space Boxcar has put between the different plates, to start with I will sometimes cut them apart without worrying about doing anything except not cutting the crop marks.
The photopolymer material is quite slick so I ALWAYS tape it down. EVERY TIME. We bought a light table for $75 off eBay like printers use to use with a gear-driven straight edge. It is covered with that self-healing kind of mat.
Remember: TAPED DOWN. Then I use a plastic drafting triangle to butt against the two outside ends of the crop marks. I do this by sliding the triangle up against the BOTH ends of the crop marks. Then I trim along the triangle and likely cut JUST into the raised crop mark. I try to push it with the same pressure every time. I then trim the photopolymer down with an Xacto knife. I can judge how well I’m doing by feeling the knife cut through the very end of the crop mark. I cut all four sides of every plate.
I take the smallest Ziploc bag that will fit and I write the name of the project in Magic Marker on the outside. I trim the proofs also. I put the most obvious proof for what the job is facing the front of the Ziploc bag to make it easy to locate.
You’ll also notice from the image below that we also show the colors on the plates. We try to think out the sequence we are going to print the colors before we make the plates. We put a line of text in 10 point and if there is a specific PMS color we will make that the text. We will then set the color to the SPOT COLOR for the plate. If you put the PMS color there it will be there if you need to reprint the job which helps you keep that kind of information nicely organized. We sometimes make plates without knowing exact colors so we will just say “FIRST COLOR SECOND COLOR…”.
By doing that when you print each succeeding color you’ll see the colors keep filling out that line.
You need to keep that type INSIDE of the very ends of the crop marks by a couple points to be sure you don’t cut them off or that they don’t affect how well you can align the triangle before trimming.
One other point to try and keep the cost as low as possible while making our plates is to set the size of the file using ‘document set up’ (we mainly use Illustrator or InDesign on a Macintosh) to a hair larger than the actual image. We do this by doing a COMMAND-A to select everything. We notice the dimensions of the selected image. We change the document set up size to a slightly larger size (maybe 1/10” or 1 pica). We then adjust the image to fit INSIDE that size.
That all got more complicated than I thought it would be. I hope it makes sense. If people ask questions I’ll clarify appropriate parts.
I’m not sure if this is the best way to store the plates, but it is how we do it. It is to keep extra air out of the bag that we like to use the smallest Ziploc bag. We put the trimmed proofs and all of the plates into the bag. We then pull it up to our mouth breathe into it five times. This adds a bit of humidity to help keeping the plate from drying out. Then we flatten the bag as much as possible and reseal it.
We also hole punch a small hole and keep it hung on a nail near the press while the job is in production.
Enjoy. It is a system that works great for us.
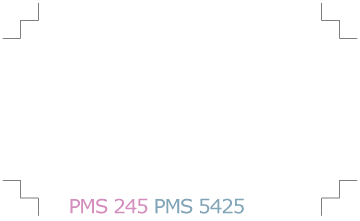
temp-registration-marks.gif
The registration marks that we use for photopolymer plate production are two 1/4” long lines at 90 degrees, each pulled back .0625” from the vertex (placed in each corner, obviously). So I guess it is similar, except we don’t have the additional two lines connecting them, and they aren’t pulled back quite as far.
I guess an advantage to pulling them back further would be reducing the chances of getting any ink on the corner of the finished product if you can’t guarantee precise printing or trimming. Any others?
Do you think that the two additional lines help you align multiple colors? I wonder if their similarity might make me second guess where I would be making a cut—it’s pretty obvious if you think about it, but maybe not at a first pass.
I REALLY like your idea of putting information in the crop mark zone.
Does any one use an asymmetric system so that they can only line up one direction? Something like an extra registration mark on the middle of just one side? Or having one registration mark different from the rest?
I believe the register marks available in postscript output dialogs in PS and AI are offset so you can only register one way. I was using them as guides for centering a print on a large piece (they afterwards were trimmed) and the print ended up off centre as they are not symmetrical.