Reproducing old dies
Hi all,
One of my personal passion (besides collecting and restoring Golding presses and collecting wood type) is collecting and printing with the old ornate dies of the mid to late 1800’s. Recently I purchased an ornament and border case from this period filled with some beautiful electrotypes. I have identified some in the Marder & Luse specimen catalog from 1881. Now, to my question: Is there a recommended method or best practice procedure for me to have a copy or several copies of these highly decorative electrotypes made? A typical problem is having only one, two, or three corners out of the four needed, or having some damage on one or more corners which limits usability. These electrotypes are copper on lead which obviously isn’t being done today(to my knowledge), but, can a faithful reproduction be done with copper on wood? Is there a way to reproduce without losing detail? I can only envision having to make the best print I can get on good paper and then scanning it to send a electronic file to produce traditionally. When I scan it, it will have to be converted to a bitmap and I wonder how much detail will be lost in the whole process. Is there another method I am overlooking to get from electrotype to file? If not, what is the absolute best method or settings I can use to retain as much detail as possible using traditional scan to file and then bitmap conversion? I don’t mind experimenting but it can get expensive. I then wonder about getting a precise matching shape to the original. Has anyone asked places like Owosso to cut the wood die to precise “L” sizes/shape(for corner blocks), or is this better left to me and just get the block large enough to trim myself. This is not something I can find a resource covering and thought I cannot be the first to attempt this. Here is an example of the kind of dies I would like to reproduce.
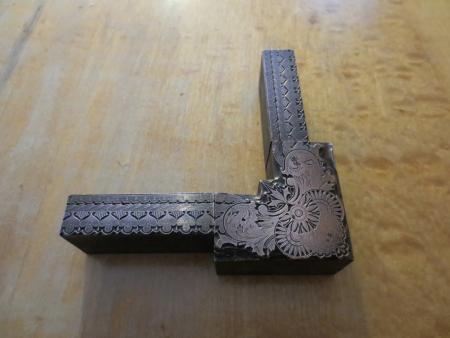
IMG_0227.jpg
Am i reading this right, you want to print these????
I’d suggest you have them mounted oversize and do the trimming in your shop with the Glider saw. You don’t want to have to put the original in the mail and nobody’s attention to detail will be better than your own.
Just a warning- Owosso’s wood backing material isn’t what it used to be. I’ve seen a lot of issues with warping over time.
The other possibility- when you use these, lock up furniture in the corner where you are missing one, print what you have, then move one to the last corner and print it registered to the rest. It’s more fiddling around, but it will keep you from having to spend the bucks.
DGM
If I’m understanding the question, you would want it to be vectors to avoid the fine detail being lost in the bitmap file. You’d have to scan and then redraw the entire thing (well, half of it, then mirror that) in a piece of software such as adobe illustrator. It would be a bit of work, but then you would have a file that would produce smooth details and that you could scale to any size without issues.
I would like to add a couple of comments. When I started in the print production business, we still had galley proofs made from metal on repro paper which was pasted down and shot with a Robertson Wall Camera. After scanners came in some art was scanned. More recently we have done scans at 2500dpi to convert to bitmaps which is then output to film. The detail is there if the original is sharp enough. One caveat is to make sure the scanner bed is large enough so the corner piece doesn’t get distorted. Bottom line if you have access to a high end AGFA or other flat bed scanner, you can hold the detail.
John:
I would do proofs on good coated paper and scan in as longday suggested at a high resolution. Then you can do some touch-up work with a graphics program to repair any defects or voids. The file can then be sent to the engraving company to have cuts made. It might make sense to cut apartr yourself so you can nest images within others and cut apart with a band saw later.
Do you have access to any honeycomb or other patent base? If so, you can get the engravings done in 11pt. or 1/4” metal and have no worry about the base deforming.
John Henry
Back from lunch!
dickg: Yes. (for those that don’t understand this exchange, dickg doesn’t think I own any ink because my presses are quite clean.)
Daniel: I agree with your points and love the idea of a second lockup although I must confess, I would be more comfortable doing that with my wood borders than the metal because there seems to be less room for error and still look good with the metal.
Kimaboe: Thanks yes, what is the best input device in your opinion for redrawing in Illustrator?
Longdaypress: Thanks for sharing your experience. I don’t consider my scanner to be high end but do have the higher resolution capability.
John Henry: I realized soon after posting it was silly to ask about the cutting. I don’t think we have the support infrastructure to expect that kind of accuracy and special shapes as its not likely in demand. I’m not as concerned about the cutting as the detail issue and I can do the job in my shop. It seems as though there is really only the print on proper paper and scan method with high resolution, and good file preparation. I wanted to be sure I wasn’t overlooking something obvious given my lack of experience.
A honeycomb base with toggles is on my list of wants as I also recently acquired a really nice (full) four color/plate lily image I want to try. Talk about a challenge. (Might be the farthest thing from todays normal interest of deep impression.)
Thanks everyone,
JF
JF
As Longdaypress mentioned, a high-resolution scan is probably going to be perfectly fine. As a designer, I’ve spent a lot of time in illustrator tracing things, so I would probably do that out of habit :) using a mouse and patience.
It would also allow me to make a huge cut if I wanted to :)
Not sure how you would need to prepare the artwork, but have you looked into the laser engraving of hardwood option? I’ve seen some pretty intricate detailed designs done this way.
Or you could try recreating the electrotype process, which might not be as hard as it sounds. Basically you need a matrix (the early technology used a wax sheet, later it was a plastic which I believe was heated as it was pressed into the form to make the mold) in which to plate copper, after coating it with a liquid graphite for conductivity. After the shell is thick enough pour hot lead into it, then machine off the back to the correct height and mount the cut. You could go with metal base for stability, or something like Delrin sheet stock.
Should be a piece of cake (NOT!).
Bob
emthree: I have read a lot about laser engraving when it gets discussed, but, we are talking some really fine detail here. Think of a old stock or degree certificate detail. I may be wrong, but, I don’t think it could get that fine. If we were talking ATF borders and cuts it might be appropriate.
Bob,
Now your talking. That intrigues me to know end, having recently worked through casting issues with polyurethanes using silicon molds for making Golding Pearl drawer pulls.
JF
John, it sounds like Bob is set up for making electrotypes, just let him do it for you.
The way I would have had this done years ago, as I suspect many of us would have, would be to pull a repro proof of the original electrotype using matte coated proof paper on a Vandercook. Then I would have given the proof to an engraving house who would have shot a silver based negative using lith ortho film and made a line cut. Is there no engraving house with a process camera and film processor any more? Something tells me that there may be a few left because I looked on the web and found two suppliers of lith ortho film. What would graphics people use this for if they didn’t use it for offset or letterpress platemaking?
One other point to your original query, John. If you are going to reproduce for instance, one corner piece, perhaps it would be better to reproduce 4 corners and enough straight pieces to print the whole border from reproduction engravings. I can think of two reasons for this. First, you won’t cause wear to the very rare originals, and second, if you get just one corner, it may not have the original line thicknesses perfectly reproduced, resulting in the one reproduction piece being slightly lighter or slightly bolder than the original border pieces.
Please keep us posted on your progress. To me there is nothing greater than bringing a long lost part of printing history back to life.
Best regards, Geoff
You could also possibly recoup some of your costs by selling copies of these wonderful old cuts to those of us who are also interested in them.
If you’ve got a vacuum chamber you can use with your silicone casting, you could likely get very good quality moulds. If not, all those little details are likely to trap air and make all kinds of problems.
Once cured, you could cast one in either silicone or something harder like plastic just to see how the mold came out. If satisfactory, you could use electrodeposition (heavy duty electroplating) on the silicone as mentioned by Bob to build up a copper layer thick enough to mill down flat in the back and mount to wood. No need for the intermediary typemetal layer. That was just to make the cuts less expensive.
Incidentally, this is similar to how many of the casting matrices were manufactured for print-room machines like the Monotype & Thompson casters and even many foundry mats for machines like the ATF Barth casters. A master (whether an original from the type design department or a piece of competitor’s type) would be locked up in a special mould frame, coated with a thin layer of graphite as a conductor/mould release, and a matrix blank called a planchette with a hole in it for the actual letter mould would be locked up against the face of the master. Copper would be electrodeposited in the hole until it was thick enough to mill back to flat.
David McMillan has a detailed write up on his site, complete with pictures, from a demonstration on this technique at an ATF conference a few years ago. I’m unfortunately not finding the link right now, though.
For the material on electroforming matrices, see:
http://circuitousroot.com/artifice/letters/press/typemaking/literature/e...
The best article yet written is the one by Mike Anderson (which he has kindly allowed me to reprint, at the page noted above). I do now have permission to reprint Duensing’s edition of Nuernberger’s letter to Archie Little on the subject, but have not yet done so.
There may be issues in electroforming something as large as John’s borders. It has been done - there is a photograph of a huge electroformed Ludlow border matrix of unknown origin in the ATF Newsletter No. 33 - but I don’t think it was ever common in such sizes. (It was *very* common in display type sizes and smaller.) I’d also be very wary of using a unique original in the process - better to work from a copy, as mephits suggests.
Regards,
David M.
www.CircuitousRoot.com
Mike Anderson has become expert at electrodepositing mats — he’s created several entire fonts that way. I bet he did the demo for ATF.
The plating time to build up an entirely copper plate would be very long — and take a lot of energy as well as a lot of copper. The electros backed by type metal are as strong as the copper and much faster and cheaper to produce.
I’m a little surprised there is not one single electrotyper still functioning somewhere — probably is in India somewhere. The two problem areas to recreating the process are the mat press and the milling machine for the backs of the plates. Getting good wood for mounting is really just a matter of careful selection.
Bob
Yes, Mike Anderson did a demonstration of electroforming at ATF 2010 Piqua. He’s an amazing guy. Most of the photos I have online are of his process and equipment. What is most impressive is the way in which he has simplified the process and its equipment to an “anybody can do this” level.
>The plating time to build up an entirely copper plate would be very long
Typically the electroformed portion is grown into a hole in a prepared blank mat (“planchet”); even Starr’s original 1845 patent describes this process. It’s also easy to see on a standard Lanston Monotype display mat. I am aware of only one person who grew the entire matrix in solid copper - the late Andrew Dunker. His mats are just stunningly beautiful. Dunker’s mats are also unusual because he used a metalworking shaper (a reciprocating machine tool unrelated to the woodworking “shaper”; now considered obsolete, but still a great favorite with amateur machinists) for machining the mats. You can see the telltale fine straight (not curved) lines of the shaper’s single-point cutting tool on the mats. These, in turn, cast a fine pattern of parallel lines into the (non-casting) shoulder of the type.
The large electroformed Ludlow mat shown in ATFNL33 was made as a thin electroformed shell backed up with typemetal. The related process of making relatively large working patterns for pantographic engraving by electroforming over a wax-on-glass original typically also involved a thin shell backed up with typemetal. (LB Benton would seem to have introduced this process in the early 20th century; it was one of several different processes ATF used over the years. They never documented it, but the English Monotype company did document their version of it.)
Regards,
David M.
www.CircuitousRoot.com
The electrotypes look worn and probably have a few scratches/dings to boot. The best course of action would be -
Pull as sharp and clean a proof as possible.
Scan the proof and put it into Photoshop.
Seriously enlarge the image in photoshop and go about sharpening and repairing any damage.
Reduce back to original size and send to Owosso for new engravings.
Simple and effective.
Rick
Thank you all for your comments and knowledge on the subject. I am going to do a lot more reading/investigating including what was suggested and see where I can go with this. I have been offered additional help off list as well. I wish I could take a picture of the case to show you how beautiful they are, but, I had to make the purchase a birthday present to get the wife to agree, and the day is not here yet! She let me take the one I photographed out to stop my whining. I’m not supposed to even look at the others yet. I told her, ya know I’m getting old and anything could happen. How would she feel if I didn’t make it to my birthday and she kept these from me. She didn’t buy it. I have to wait.
JF