Advise on printing paper bags
We have gotten a job in house that involves printing on paper bags. Since we have not done this before I thought I might get some advise first.
Would a Polymer plate or magnesium plate work better?
I can print on a 8 x 12 C&P (which I think would be my choice) or a 10 x 15 Heidelberg Platen, or 12 x 18 Kluge.
The bags are 4.25” x 11” flat (folded like a brown bag for lunches).
I realize the makeready will be the most crucial step as I need to build up in the center of the bags to compensate for the sides folded in, as you can see in the sample image they want printed.
Thank you all in advance for your help.
Jim
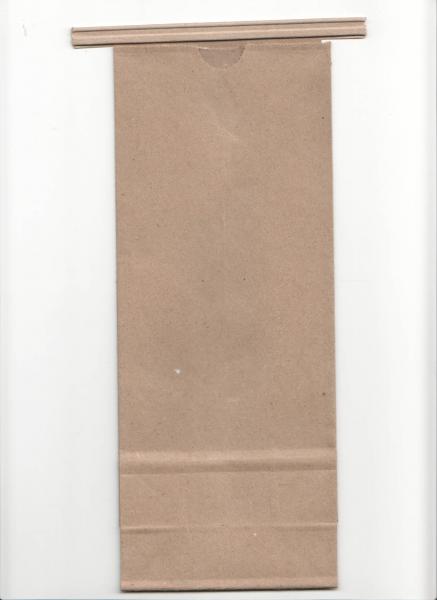
Print_Side.jpg
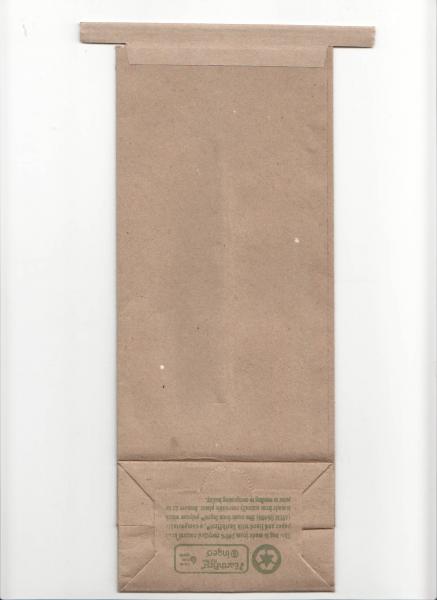
Non_Print_Side.jpg
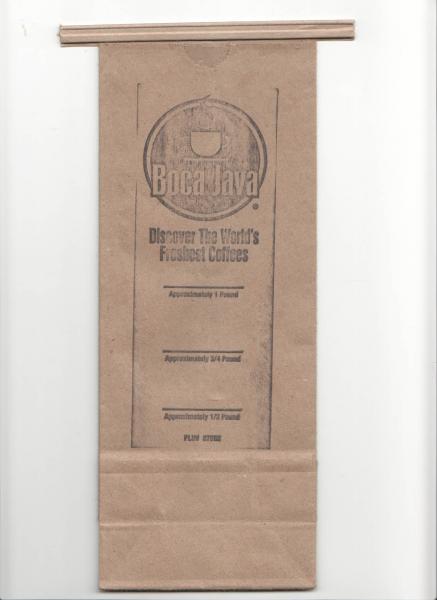
Sample_Image.jpg
I printed bags like these long ago, ran them on my windmill, set the type Ludlow, cast it 6 times because it was a 10000 run. Before I printed 200 bags I had smashed 4 forms, all the makeready in the world didn’t help, one crooked bag or one that isn’t folded just right and your type is junk. I ended up making a rubber stamp of the form, ran the job for 5 years with the same rubber plate. Maybe a soft polymer plate would work, I don’t think a mag die will stand up very well.
I use to print bags for a bank. They were the heavy bags you see at hardware stores. (or, use to see) The bank used them for coins rolled up. They had several branches of that bank. I would print a lot of bags. Like Dick says, your type will be pretty much junk afterwards. I started using a mag plate for a while. Afterwards I went with a rubber stamp die mounted it type high. Printed away with it in the press for years.
Winfred Reed
Black Diamond Press (Kentucky)
Where can I get a rubber stamp plate made?
I’ve printed wire tie bags of about this size and a couple things spring to mind:
These can run on a Heidelberg Windmill, but some paper bits will need to be taped onto the feeder so that the wire ties don’t hang up and tear off.
When running on a platen (I’ve heard of folks printing these on a Vandercook), make sure not to let the press idle too long (more than 3 cycles, or the ink tack will become so great the bag will pull out of the grippers and crash.
I’ve printed these with magnesium plates, but they have to run on a metal base. I ran a 4 x 6 image in two colors and the wood bases were pretty much destroyed after a 1000 print order. A subsequent run was done on a metal base and the plates were in good condition at the end.
Bags require fiddly makeready, which was not done in the images above. Rubber sheet is handy for this.
This job is in the upper end of what I feel comfortable running on a 10 x 15. I would be leery of running this on a 8 x 12 unless there was very little image area.
If you are running a substantial image, and a large quantity, a fountain is very handy. Low tack ink is also a necessity.
I would hand feed unless you have a resilient forme like a rubber stereo. Are these still made? I printed thousands of envelopes on Heidelberg platens, and its damaging because of the inevitable smashes because of mis-feeds. When the envelopes come out of the box you need to manipulate them to break glue joins etc to get a reasonable feeder pile. Better to hand feed if you can.
We just started running coffee bags for a roaster based out of Tulsa, right now we are doing about 1,000 bags a month but that could increase soon. The first time I used a 10x15 Heidelberg platen and I was able to print with guides on the front but the back didn’t have enough margin with the plate so I had to run it commercial which was a nightmare. I really don’t think two bags are folded the same so without guides, if they were off just a hair, it really shows due to the folds in the bag not landing on my makeready build up underneath the tympan paper. I had a strip of 100lb cover for the center where the bag is thinnest, then I had different thicknesses on either side of that due to a second fold on the far edge.
I really found that on the Heidelberg I couldn’t feed more than 10-15 at a time because of how awkward the bags are when they are laying on the feed table.
I am also using a magnesium plate but watch out for misfeeds, I had one one bag that was curled from laying in the shipping box weird and it missed the guide and fell and then the next bag smashed into it and damaged the plate a little bit so be careful of that. Next round I will probably print the front with the Heidelberg and handfeed the back for better registration.
Hope this helps and good luck.
Here’s a link to a video - http://instagram.com/p/mB9VR-pEBV/
I’m way out of my depth here, but I think any supplier to the flexography trade can make rubber printing plates. Call one near you to discuss what you need - they will have the answers.
Look up Flexographic Worcester, MA. They can make the rubber plates that you need. I’ve been to their plant. They made some magnesium plates for me and saw some of the rubber plates being made that will do the job for you. Sorry lays posting otherwise I would have the contact info for you. Ted Lavin
I’m curious about the rubber printing plates. Do they print essentially like rubber stamps - somewhat smeary and blobby? I do a job like this a couple times a year. I run it commercial feed and find the variance isn’t enough to notice. Makeready is a b&$Ch, though!
I think anyone who makes printing plates can make a softer plate for you. I have made rubber stamps then mounted them type high and had great luck printing them, when I print anything that requires makeready like envelopes or bags I remove my tympan and packing and replace it with a rubber blanket, mostly use ABDick blankets used on offset presses. This way if one goes crooked the rubber has some give and you don’t smash your type. Also makeready is easier, sometimes you can just squeeze it a bit and the form will look great even without makeready.
Well, we ordered a photopolymer plate from Boxcar Press. Used an offset blanket for packing, and started to print.
Look at the photo to see how the bags look now, our customer is very happy with them now.
Thank you all for the input and advise, this site is GREAT.
Jim
Final Sample.jpg