Shaft creeping out of Pearl OS 7x11
Hi all,
I was hoping that someone who has worked on presses before with a mechanical mind can help me out with this one. I bought my OS Golding Pearl back in February and have used it quite regularly for large and small jobs, and it’s been working perfectly. Recently I noticed that the shaft that holds the hinge together (basically joining the platen and the body of the machine) has started to creep out the left side of the press and is getting dangerously close to the flywheel. I wish I could tell you that I saw it happen, but I noticed it after a few huge jobs that I had done recently. Unfortunately trying to simply push it back in isn’t working, it’s stuck, most likely because of the pressure bearing down on the shaft. Because of this, the shaft is no longer holding the right side of the interlocking parts together and I’m afraid it will snap. Please take a look at the images I’ve attached, they’ll probably be more helpful in explaining the problem. Thanks ahead of time for any advice!
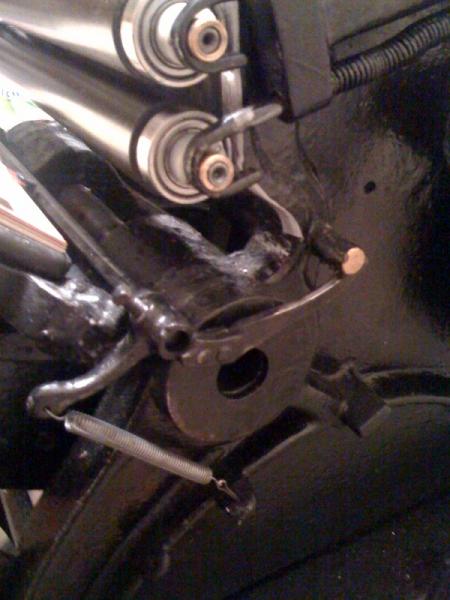
photo 2.jpg
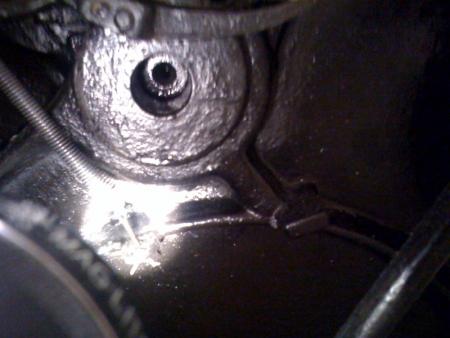
photo 3.jpg
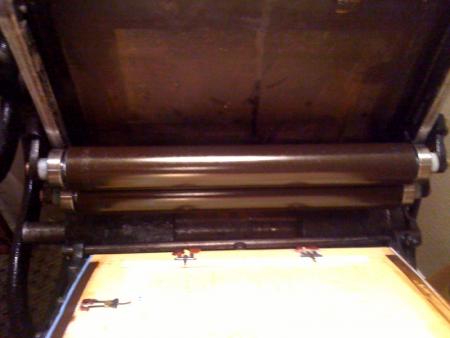
photo 4.jpg
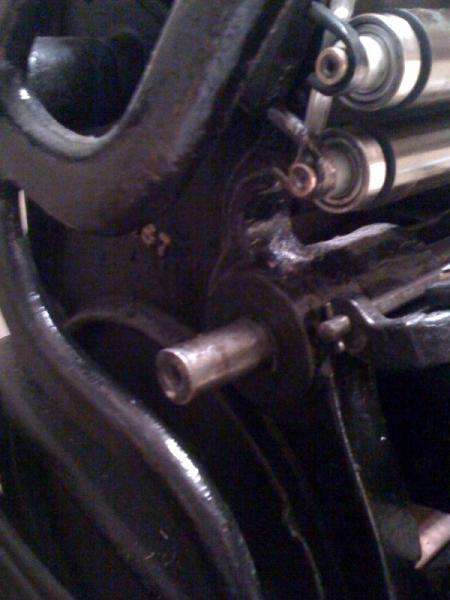
photo.jpg
Do NOT operate the press this way — you’ll damage it if it isn’t already hurt. If the shaft has come completely out of one end bearing then it is mis-aligned and that’s why it won’t go back in. Look closely in the empty bearing and you should be able to see the end of the shaft and which way it’s mis-aligned. Probably your best bet is to carefully wiggle the platen in that direction while tapping lightly on the other end of the shaft with a plastic mallet or with a block of wood between the shaft and a hammer (it’ll probably require two people). Once you get the shaft started back in the bearing it should slide in readily with more tapping on it. There should be a set screw there somewhere to lock it in place — if not you could add one or just watch it carefully and push it back in place when it works out. If the holes in the ends of the shaft are threaded there were retaining screws with large washers that are missing, that would hold the shaft in place. I’m not sure how the press was originally equipped.
Bob
Never take mechanical advice from me. That said, here is a photo of the same region of my Pearl No. 3. I am pretty sure my Pearl has all original parts, and the shaft on mine looks different from yours—it has a slot in each end, presumably from a screw that keeps it in place (???). (Since it hasn’t malfunctioned, I’ve never inquired too closely into its purpose.)
pearlside.jpg
AdLibPress: Thanks for the input. Everything you’ve said is what I’ve imagined I should do - it came out somehow, so it should go back in. I’m afraid that the worst case would be that the shaft has bent - then I’m screwed. Another thought was to also turn the flywheel inch by inch and hope that at some point the pressure will be taken off of that hinge so that it can slide in more easily. At the same time wiggling the platen as you’ve suggested.
Clothdog: Ok - mine never had screws like that on either end, so I suppose it was a matter of time before this happened. I wish I could’ve foreseen this and added something to prevent this from happening, but hopefully if I can get the shaft in place again I can find similar screws for either end (especially since the threads do exist as AdLibPress suggested).
Thanks! Any other advice is greatly appreciated!
I’d bet Mike Anton can supply you with replacement parts to fix this. You might want to ask for a replacement shaft in addition to the end hardware.
Daniel Morris
The Arm Letterpress
Brooklyn, NY
Clothdog, from your picture it appears that you have the wrong size shaft for your gripper bars. Since the end of the shaft is painted blue, it looks like someone went to a hardware store and got a piece of steel round bar off the rack, which was color coded on the end.
I just measured the gripper bar shaft diameter on my Pearl #3 and it is 3/8 inch. Yours is probably 5/16 inch. Your shaft might cause abnormal wear over a long period of time. As for me, I like to see everything repaired and working as closely as possible to the way it was originally designed.
Hope this helps………..Geoffrey
Hi Jabazigos,
Might as well get my two cents in here as well. You have been given very good advice from knowledgeable people. The only thing I might offer is that Golding made their shafts out of pretty good stuff. It is possible, but, not likely that it is bent. The end may have gotten some minor damage that is keeping it from easy reinstall if alignment seems good and you are still having trouble. It may prove better to remove the shaft entirely in the direction it has wanted to go, clean it thoroughly, chamfer the edge that you will be inserting with a file, lubricate it with a good oil, and then try reinstalling from the same side it came out. Once in, get proper screw/washers installed to prevent it from happening again.
John
Geoffrey, you are right—I have the original shaft but actually almost never use the grippers (No. 3 grippers are just a pain, in my opinion), so they are usually lying in a drawer. The original shaft is very lumpy and sticky and doesn’t allow me to slide the grippers themselves easily, so rather than spend time fixing it, I had a piece of metal cut for the few times I do use them. Egad, I had totally forgotten that! I did use them not so long ago and just left them on. You have a keen eye. Let no one try to pull one over on you.
Update: so my husband and his friend have been at it for a while now. One of them is lifting up the right side of the platen where the shaft has backed up, to make it level, and the other is hitting it at the end to try and get it to go back in - nothing is happening. They even tried pulling it out as John suggested, but it won’t move in either direction. It also looks like when you turn the flywheel, the shaft is attached to the platen and it moves with it, but freely moves through the hole in the body of the press. Thoughts?
try putting a pipe or something in the hole where the shaft came out, wiggle it while someone tries to push the shaft back in, if this fails call John Falstrom. Dick G.
My Pearl doesn’t have any hardware on the shaft ends, it’s free to slide from one side to the other and will do so easily with the tap of a mallet. It will wander a little protruding now and then if I print with a heavy impression, (which I hate doing anyway.)
My shaft is not tooled to receive any hardware either, it only has the little dimple remaining from being turned on a lathe.
I had to take my press completely apart to get it up three flights of stairs by myself to my home and it went together easily.
I bet it’s just still out of alignment, it has to be PERFECTLY aligned or it won’t drive in. I would get a flashlight and peer down the hole and see if you can see any lip showing where the platen and sideplate meet in the hole. while someone tries to gently tap on the end.
By the way Clothdog - I would love your grippers, I only have one and still use it all the time to print on text weight papers and oversize sheets.
Hi again,
I don’t know if you are using the word “pull” literally, but in my experience of taking apart Golding presses I have seldom had a shaft I could pull or push. They usually require tapping with something that will not hurt them. It is also important to have all the parts lined up while tapping as Dick suggested. I would suggest you get a wood dowel as close to the size of the shaft as possible(but smaller). Thread it through the parts with the empty holes until you meet the end of the metal shaft. If the dowel is close to the size of the shaft, this will line up the parts. Apply something like Liquid Wrench to all oil holes that impact the stuck shaft and any spot where you can get it into the effected parts. Tap on the end of the wood dowel and see if you get some movement. You can try to go either way, but, if it were me, I would be trying to tap it out at this point to do what I suggested in previous post. Dick’s suggestion is also good for lining up the parts to try to tap it back in. I would not try tapping the pipe to move your shaft out as it would be metal against metal. Some shafts are partly exposed and get dirt, ink and other stuff that builds up on them over the years. If they are not held in place and begin to move, this accumulation can make it difficult to remove or return the shaft to its original position. It is not attached to either part involved in the connection. It is just being stubborn. Keep applying a product designed to help loosen joints, line up all parts, and tap. That is the best course of action to my knowledge. The direction you tap is up to you. Even tapping one way then the other may help.
John
Another trick to try would be to see if you can get an accurate measurement of the shaft or hole diameter (if you’re lucky it will be a standard diameter) and get a piece of drill rod at a machine shop that’s a bit longer than the present shaft. Chamfer one end of the drill rod about 1/8 inch or so with a file, or have a machine shop do it on a lathe. Then carefully slide or drive the rod into the open end and when it gets to the platen it should work itself into the bore of the platen — you will probably need to wiggle the platen a little to get it started. Then use the drill rod to drive the original shaft out, where you can chamfer it and find some screws and flat washers (large ones are called fender washers) to fit. Then you can reverse the procedure, driving the old shaft back in and pushing the drill rod out at the same time. Assuming the old shaft isn’t damaged, you should be good to go. And if you were lucky and the standard diameter drill rod worked, you can cut it off to the right length, have a machine shop drill and tap the ends for machine screws, and use it as the replacement shaft. Drill rod is tool steel and precision ground so if it fits it’s probably better than the original.
Bob
Regarding the use of drill rod or tool steel for a shaft, I would not use a shaft which is harder than the original one. If you use a harder shaft, then the castings which the shaft turns in, are more likely to wear. In this case, you want the easy-to-replace shaft to take the wear instead of the hard-to-replace castings. This means the shaft should be the same hardness as the original, which is probably fairly soft steel, like mild steel.
Part of the engineering which goes into designing a machine, is carefully choosing materials and their hardnesses so that the wear takes place on the easy-to-replace and/or inexpensive parts. Changing the hardness of replacement parts, in most cases, is not a good idea.
Hi all - thanks so much for your input, I greatly appreciate it, and am so happy to see such helpful people in this community. Good news - we got it back in! All it needed was some patience and a bigger lead hammer to really drive it in. Now I need to get some screws for each end to make sure this won’t happen again and I’m good to go. Thank you - I feel complete again :)