Damaged C & P Rail
Friends,
Looking for some help here. Last night I spent a few hours trying to help a friend with her 8 x 12 C&P Old Series.
She was having a problems while printing a cut. Although she had a deep impression throughout the cut there was a certain area that was not taking ink.
We examined the delrin trucks and found that they were slipping on the cores, having not been pushed far enough into the nick. She had a serious amount of tape on the rails in order to bring the rollers up to type high. Upon further experimentation we substituted a set of Morgan Expansion trucks, re-adjusted the rollers removed the tape and got a pretty consistent image.
However we discovered that both rails had a pretty serious indentations around the same area. I believe this causes the truck and rollers to bounce and or slip when they go over the dented area. I have attached a pix and you can see the depth of the dent behind the white line. I’ve never seen anything like this before and can’t imagine what could have caused it -on both sides!
Is there any way to repair this. I was thinking about clamping rule or a straight edge to either side of the rail and filling it with JB Weld then sanding to the rails proper height.
Can this work, are there any other tips out there on how we could correct this problem?
thx
Steve
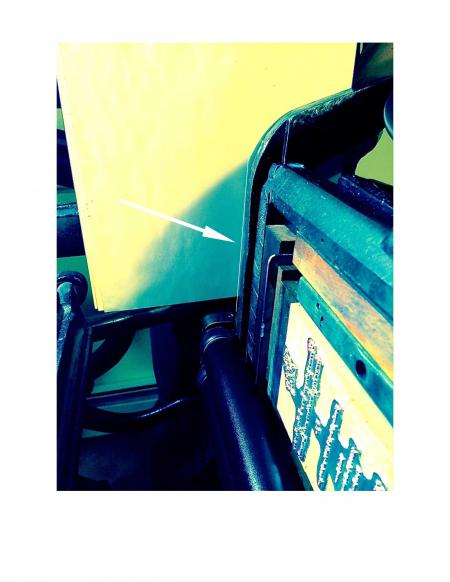
Dentedrail2.jpg
Steve, Tympan bales more than likely caused this.
I use nylon washers outside the truck with a little wiggle room before the saddles, this keeps the trucks from walking. Have you tried using a combination of your
derilin truck and a mert? best james
Allright; you can repair this with simple materials you can get from a hardware store and make the press work just as well as it would have before the dents.
You need:
~A lawnmower blade sharpening stone (shaped like a disc- 2 sides: coarse and fine).
~3 in one oil.
~Acetone (for degreasing after grinding)
~JB weld.
~a straight edge razor blade.
Anytime metal is dented, there is generally both a convex and a concave portion of the dent. The metal will sink in and also raise up a little around the sink. First, get a straight edge or machinist’s square and some tissue paper and determine if the dent has a raised portion; put the straight edge against the dent with the dent located in the middle, and a piece of tissue paper on either side; hold the straight edge down at the dent and pull the tissue paper for slippage. Next, put a piece of tissue paper over the dent as well, and repeat; if the paper at the edges slips easier on this second check, there is a raised portion even if you can’t feel it.
You can also just put the straight edge over the dent and check for ‘rocking’, and that will let you know; be sure to clean the area thoroughly before inspecting, as even dust or anything on the surface can give the false impression of a raised area.
If it’s raised… It’s important to return the metal to flat by lapping the entire face of the rail to one height. Don’t think you can just sand down the raised metal at the dent; it won’t work. You’ll create a dip.
The only real way to flatten out the dent is to grind from the top of the rail to the bottom of the rail, repeatedly, and consistently, with pressure the whole way along.
Use the coarse side of the lawnmower sharpening disc and put some 3-in-1 oil on the rail, to aid in ease of sliding and also to keep filings from getting into the air. This will keep the stone ‘open’ and working as well.
(Also, wear some protective gloves for your hands- thin gardening gloves will do, the kind covered with neoprene are best. Don’t bang your raw hand against the press in that tight space!)
If you work back and forth about 30-40 times you should see the raise decrease, and as long as you are consistent you will not take the rail out of true.
Filling the dip:
Next follow the JB weld or epoxy directions for prep, and fill the dip with a small amount- taking care to de-grease the area with acetone or some other strong solvent before applying the epoxy/weld.
Scrape it level with a razor blade while still wet, but leave a little bit on top to take off after it is dried.
If you use the razor blade in a holder to take it off AFTER it is fully cured, you can get a really flat surface.
I have repaired aluminum vacuum tables this way, and more than one C&P rail that had a similar dent. If you have questions feel free to email me.
Posted several times previously, scrap all the myriad of methods for taping the rails, just construct a pair of stainless steel slippers to exactly fit over the rails.
E.G. 15 gauge equates to approximately .064 (sixty four thou).
Fashion them over any piece of suitable hard material gripped in bench vice, formed into *C* to sit on and over the rails with tiny Tounge as run on & run out at each end for the trucks to follow
.
If the *Jaws* of the C are biased .002 - .003 IN they will clip on AND/OR mjnute touch of super glue under each Tounge.
Job done permanent solution, throw the tape away
,
If the rollers are raised slightly too much, NO problem, merely pack the form/chase with litho plate (approx .006 Thou) or acrylic sheet(s) in wide range of thickness(s)
Virtually perfect as make-ready for Printing heavy forms, Cutting/Creasing and especially Perfing to protect the Bed!!!
N.B.15 Gauge in flat form can possibly be dented with small hammer with sustained blows, but in *C* section will withstand a lot of punisment.?
I’ve a booklet entitled: Pressmen’s Hints, from 1934, that describes the rail treatment pretty much as you’ve described, Hank54. (The securing of the rail differed slightly from your descript in that it involved tapping into the side of the bed.) I have used such method myself to affect press repair on more than one occassion.
Somewhere along the way, though, the use of tape rose to be accepted rail fix. That it has/had obvious disadvantage seemingly did little to dissuade its users from this ad hoc repair. And for the same reason people eschew forme bearers, your approach will be dismissed as well. The reason, you might ask? Too many have no idea of how their press operates, expect instant result from these elderly machines, all too often substitute over-inking and excessive pressures to achieve what they - incorrectly - term letterpress printing, and rarely crack a book to understand the foregoing. And don’t even mention make-ready. :o)
Forme, Thank you. Yes of course variations from the original theme are several. One favoured variation was to secure *The Slippers* with 2 each tiny Archimedes type screws, as used to fix Make/Model and Serial number identification plates to the main frame etc. (beyond the Truck Track.)
And yes again, as you imply, tapping and threading the slippers into the bearers, with tiny countersunk screws outboard to clear the Roller arms if required!
Plus often with smaller Machines where the chase was close fit in the bed, without the advantage of register/positioning *Nipples*, “C” section Slipper was modified to *L* shape slipper.
Forme Thanks again, combined efforts may just get a few to think outside the box.!
Well tried and tested since `54. Hank.
Those are great suggestions, Hank- just as soon as the hop is taken out of the rail.
Haven Press, Ta!. Generally our method only had to raise the worn Rail Height and effectively bridge the low points.
The *C* section worked/works like a “Bailey Bridge”even when there is a gap under from localized wear.
The strength from the *C* section is far in excess of anything the roller return springs can exert.
If it were of concern (never tried/never considered necessary) it would seem to be quite in order to span any low spots with 2 pack Epoxy Resin or Chemical metal prior to fitting slippers.
In the U.K. in recent years we have seen much publicity regarding repairs to broken castings involving Chemical Metal implying >Filling/Drilling/Tapping/Threading< etc.
Probably Overkill for a few THOU gap under the *C* section.
Good Luck. Hank.
It’s not the gap that worries me, but the surrounding bump created by such a dent.
Read my post: when metal is struck in such a way as to create a dent, the dent does not just go inward; the metal around it goes outward. Minutely, but it does.
I would guess that this damage occurred due to a previous owner running one job repeatedly, like a numbering job, where the rollers would be lifted over the plunger of the numbering machine and drop back onto the rails in each direction, thus over thousands of impressions hammering or wearing those dents in the rails. There may or may not be a raised portion on either side of the dents if they are due to wear rather than impact. It’s sort of like erosion — over a long time of continuous repeated small impacts a lot of metal can be moved or removed.
Bob
Chris, Bob and Hank,
I am amazed at how many and how thorough the responses to this query have been. I will remind you that this is not my press, as it belongs to a friend that has been struggling with this issue for some time. It was only recently that she mentioned it to me, I’ve only seen there press once.
I would like to know more about what Hank has been suggesting. Pictures of these “C” slippers would be great.
I’m imagining that they look something like in chase roller bearers place over the rails.
Chris, you are absolutely correct, as there is a “welt” in the casting inline with the dented area just further back on the press. Sort of on the sides of rails.
thanks to all, we’ll keep you posted.
s
I am adding this pix, although it is not as sharp it actually shows the dent better.
s
FullSizeRender-7.jpg
Good thread all.
Good picture Steve. That is quite a dent.
In my teaching, I tell the student that she/he must be a little smarter than the press. Not a lot, but some.
One must understand how the press is intended to work and be able to assist it to do the job it was intended to do when new.
Building the rails up with epoxy material or installing a slipper are both good ways to remedy the problem.
I am not opposed to tape if there is uniform wear. I am interested in the beauty of the printed piece, not necessarily how you get there.
Having said that, I will say that I am an old fashioned traditionalist and prefer workmanlike adjustments and repairs to keep the old iron going.
Get some ink on your shirt.
Inky